Non-Sparking vs. Anti-Static Tools: What Are the Differences
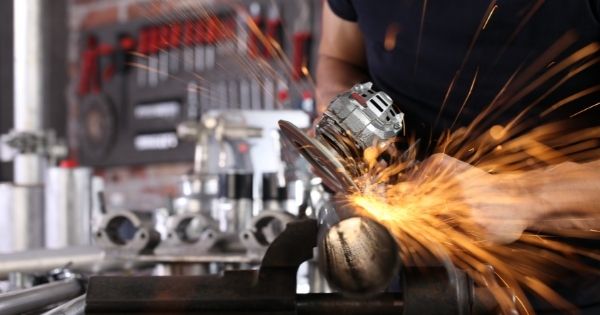
Some work environments harbor flammable or explosive materials. A single spark could result in disaster. The same can be true of a buildup of static electricity, which can create a charge strong enough to spur a fire or explosion. Learn about non-sparking vs. anti-static tools: what are the differences that matter for a safe work environment?
Non-Sparking Tools
Non-sparking tools are made from non-ferrous materials. These include all types of steel, cast iron, and wrought iron.
By contrast, non-sparking tools can be made of other kinds of metal alloys, including copper-aluminum, copper-nickel, or copper-beryllium. Non-sparking tools might also be made of plastic, brass, wood, leather, or bronze.
Spark-resistant tools are necessary in work environments that contain flammable or potentially explosive materials, including gases, vapors, dusts, mists, and liquids. While refineries and ammunitions plants are obvious places where non-sparking tools are necessary, they may also be required in food processing plants, where fine combustible dusts of flours or dried dairy products may be present.
Anti-Static Tools
While anti-static tools also have a goal of preventing fires and explosions, they’re different than non-sparking tools. Anti-static tools work within a complex system or environment specifically designed to prevent the buildup of static electricity.
Static electricity is what makes your sweater crackle when you take it off in the winter and what causes a shock when you touch certain surfaces. You can generate static electricity just by walking across a carpeted floor or scraping your clothes against the upholstery on a chair.
Some products and equipment, particularly electronic components, are extremely sensitive to electrostatic discharge. Static electricity is also dangerous in environments where flammable gases are present.
Where electrostatic discharge-sensitive materials are present, the workplace will have many features intended to prevent static electricity from building up. No highly charged materials will be present, and both equipment and workers will be grounded to keep sensitive items safe and undamaged and to avoid generating sparks that could cause a fire or explosion.
Often made of plastic, anti-static tools are designed not to lose or gain an electrical charge, so they won’t transfer or accept a charge from objects and surfaces around them. Workplaces that need these tools must maintain precise ranges of humidity and temperature for the anti-static properties to work properly.
Some work environments may require both non-sparking and anti-static tools. When you understand non-sparking vs. anti-static tools and the differences that matter for a safe work environment, you will be better equipped to protect workers and products from static electricity, fires, or explosions.